In this article, we will use Beckhoff’s EP1957-0022 to set up a FSoE safety network. The first article is just a setup and a simple program, but in the future it will be connected to various safety devices.
Come on, let’s enjoy FA.
EP1957 TwinSAFE?
The EP1957-0022 TwinSAFE component provides safe digital outputs in a module with protection class IP67 (4 outputs for 24 VDC actuators up to 0.5 A). It also has 8 fail-safe inputs for sensors with 24 VDC potential-free contacts. The signals are connected via M12 screw connectors. Power for the sensor is supplied from the load voltage UP.
In addition, EP1957-0022, which is used in this article, has safety parameters to adapt the function to each safety requirement (e.g., testing each channel).
It is important to note that safety parameters are not stored directly in the component, but are sent to the input component via a TwinSAFE Logic-enabled component when the safety application is started. This simplifies the service procedure since components can simply be replaced. Safety-related parameters are transferred to the new component when the safety application is restarted.
features
- 8 safe inputs
- 4 safe outputs
- Integrated TwinSAFE logic (same functionality as EL6910)
- Up to 128 safe connections
- Complete safety loop directly on the component
- Stand-alone operation (without EtherCAT connection)
- Standard outputs can be activated with integrated AND with safety output signals
- For applications without integrated TwinSAFE logic, the EP1957-2222 can be used.
Wiring
Here is the wiring diagram for EP1957-0022 used in this article.
Us/Up
The contacts on the M8 connector can carry a current of up to 4 A. Two LEDs indicate the state of the supply voltage.
Control voltage Us
The fieldbus and processor logic are powered from 24 VDC control voltage Us.
Peripheral voltage Up
The peripheral voltage Up provides the digital clock output, safe input, and safe output.
Fail-Safe Inputs
The EtherCAT box has eight fail-safe inputs.
EP1957-0022 offers four input modes.
Fail-Safe Outputs
The EtherCAT box has four safety outputs, each with a maximum output current of 0.5A.
Here is the wiring for the EP1957-0022 safety output.
L/A IN OUT
EP1957-0022 uses M8 Ethernet for its EtherCAT Port.
Safety Address
The safety address for EP1957-0022 is located on the back of the module.
This is the actual safety address.
LED
EP1957-0022 has several LEDs to indicate the status of the module.
Implementation
Wiring
This time it is connected with the emergency stop of Pilz.
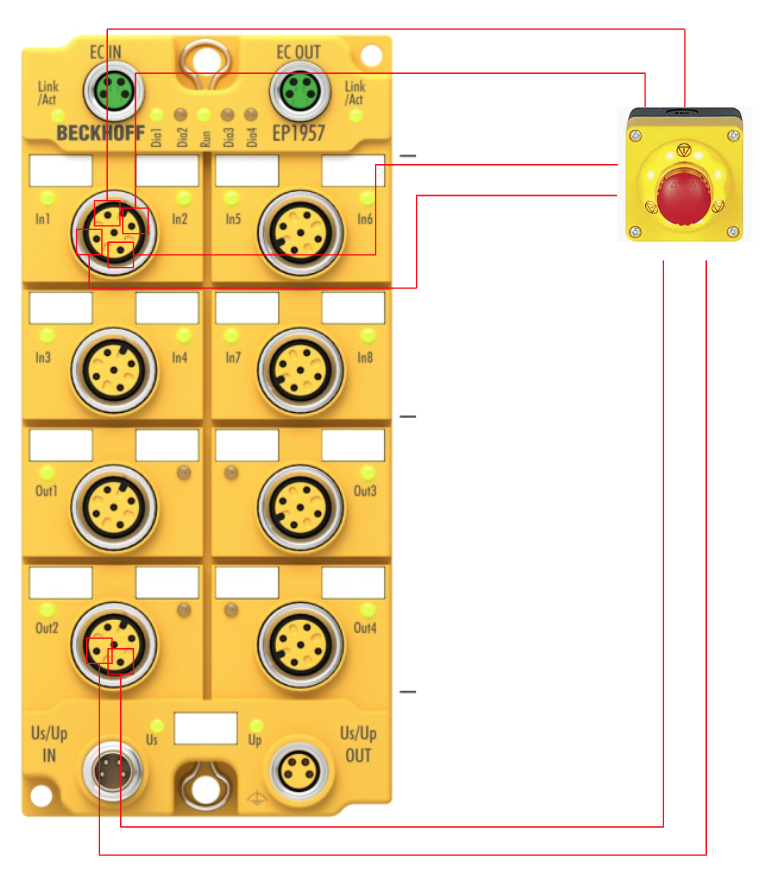
Beckhoff Side
Configure EtherCAT Master
To add an EtherCAT Master, go to I/O>Devices>Add New Item.
Select EtherCAT>EtherCAT Master and proceed with Ok.
This is the screen to configure the Ethernet Adapter you want to use as an EtherCAT Maseter, select None once and proceed with Ok.
Done!EtherCAT Master has been added.
Configure the PCI Bus/Slot
Next, click on Compatible Devices to configure the Ethernet Adapter.
If the screen shown below appears on the corresponding TwinCAT XAE, you need to install the TwinCAT RT-ET Ethernet Adapters.
Select the Ethernet Adapter you wish to use as EtherCAT Master and click >Install.
Proceed with Install.
Done!
Next, click on the Search button.
You can now use the Ethernet RT Driver that you have just installed!
Done!
Scan Network
Use TwinCAT’s Auto Scan function to search for EtherCAT Slaves in the network.
Done!You searched for EP1957-0022.
Add PLC
To add a PLC, click PLC>right click>Standard PLC Project.
Add GVL
To add a Global Variables List, click GVLs>Add>Global Variable List.
Enter a GVL name.
Defines the Process output to reset the Safety Group.
Build
Compile the project under Build>Build Solution.
Add Safety
Next, to add the Safety project, go to SAFETY>Add New Item.
Select the Template called TwinCAT Safety Project Preconfigured ErrAck and add it with Add.
Set Target System to Hardware Safety PLC and press OK to proceed.
Done!The Safety project has been added.
Target System
Set the Target System. Set FSoE Master here.
Set EP1957, which is used in this article, from the Drop-List of the Target System.
Done!
Next, click on the button in the frame and set the actual device connected to the corresponding Target System.
Set EP1957-0022, which you have just searched for in the EtherCAT network.
Done!
Finally, use the arrow buttons in the frame to Upload the safety address.
Alias Devices
To use the IO of the Block in a Safety project, add a new device at Alias Devices>Add New Item.
Select Safety>EtherCAT>Beckhoff Automaton Gmbh> EP1957… and add it with the Add button.
Done!
Configure Module
Click on the module you just added to configure the module’s detailed settings.
First, set Link Mode to Local. This is because this is the IO of the FSoE master itself.
Done!
Parameters
Next, click on Internal Safety Parameters and set the safety parameters for EP1957-0022.
Since only output 1 will be used in this article, set the following parameters for outputs 2, 3, and 4 to False.
- Diag TestPulse active
- Module Fault Link active
Link Error Ack
Now Mapping the signal to reset the Safety Group.
Click the button in the frame.
Let’s link with the GVL signal we defined earlier in the PLC project.
Done!
ADD GVL
Next, click GVLs>Add>Global Variable List to define safety Global variables in the Safety project.
We have created a GVL where safety variables can be defined.
Define IO
Open GVL as described earlier and add a new variable using the + button.
New variables have been added.
Change variable names for clarity.
Next, click on the Assignment button and set the IO to be associated with the corresponding variable.
TwinSafeGroup>Alias Devices>Set input 1 for the EP1957>Channel you just added.
Done!
Result
As shown in the figure below, we have defined variables for safety input 2 and safety output 1.
Program
The final step is to create a safety program.
TwinSAFE’s safety program is a basic FBD.
Add SafeAnd Block.
To set the SafeAnd input, right click on the appropriate Point>Change Link.
Select the safety variable that is tied to EP1957-0022, which was defined earlier in GVL.
Done!
Result
Here is a simple safety program this time, with the Safety output turned on when the two safety inputs are turned on.
Verify Safety Project
Click View>Toolbars>TwinCAT Safety to display buttons for TwinSAFE.
The next step is to compile the safety project with Verify Safety Project.
Done!There are no errors in the compiled results.
Download
Download the safety program.
Default Username is Administrator and Default Password is TwinSAFE.
The serial number of EP1957-0022 is next to the actual machine.
Select Complete Project Data and press Next to proceed.
Proceed with Next.
Check the Check Box and press Next to proceed.
Enter your password one last time.
Activate Configuration
Activate the Cofiguration.
OK to proceed.
Switch TwinCAT Runtime to Run Mode.
Login
Download the program in Login.
Proceed with Yes.
Start
Finally, start TwinCAT Runtime with the Start button.
Result
Click on Show Online Data to monitor the safety program.
Safety Group is now RUN.
Here is what it looks like when the safety input is in the True state.
You can see the actual EP1957-0022 and the emergency stop in action in this video.