In this article, we set up an EtherCAT network with a Beckhoff TwinCAT 4026 and an FSoE network with an EL6910 with FSoE Master.It is then connected to the Schmersal SFB-EC-8M12-IOP.The safety equipment will be Pilz emergency stop and light curtains and Schmersal AZM40Z-I2-ST-1P2P door locks.
Come on, let’s enjoy FA.
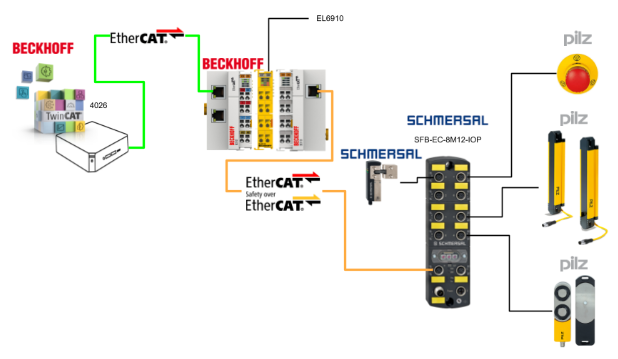
Reference Video
Beckhoff.Let’s Connect with Schmersal SFB-EC-8M12-IOP via FSoE!
EtherCAT.Let’s Talk with FSoE in 10Mins!
Reference Link
PSEN op4F-SL Series?
Pilz’s PSEN op4F-SL series safety light curtains are IEC 61496-1 and IEC 61496-2 (AOPD) compliant devices (ESPE Type: 4), which allow machinery, robots, and automation systems to work with potential physical hazardsSuitable for spaces where machines, robots, and automated systems can pose a physical hazard.
Purpose
PSEN op4F-SL series safety light curtains are ESPE Type 4 electric shock protection devices.Used thereby for the protection of personnel and systems, the safety light curtains are designed to: – Protect the operator from electric shock
- Safety hazardous areas in the building
- Safety access inside buildings with 14mm resolution
In addition, safety light curtains may be used for personal protection on machines only if
- Safety light curtains eliminate hazardous conditions.
- Machine start-up is controlled by the safety light curtain
- The safety evaluation does not specify a resolution of more than 14 mm.
Note that safety level PL e (Cat. 4)/SIL 3 is achieved only if Safety outputs must be processed in 2-channel mode for safety-related processes.
Safety light curtains are not equipped with restart interlocks.
If a safety assessment requires a restart interlock, the plant’s programmable safety system must ensure this functionality. If workers are present in the hazardous area after a protection violation, the system cannot be activated in the hazardous area.
Also, when installing safety light curtains, be careful not to go around or step behind the protected field.
This may require other safety devices or protective measures in addition to the safety light curtains. These should be determined by a safety assessment based on the specific scope of application and specific local conditions.
Serial numbers
It is important to note that transmitters and receivers must have the same serial number and must be installed, operated, and replaced in pairs.
Function
Safety light curtains consist of transmitters and receivers.By its mechanism,
- Protects transmitters and receivers from external damage
- Protects safety light grids from malfunction due to vibration
The protected area is covered by an infrared light beam, which is radiated from the transmitter to the receiver.
The beam is emitted from the receiver to the receiver. The protective area thus created can detect opaque objects.Control and monitoring of the infrared transmission and reception is done by a microprocessor.
The output signal switching device (OSSD) switches to the OFF state when one of the following conditions is met
- Multiple light beams blocked by an object, body part, or opaque object at least as large as the resolution (14 mm) covered by the safety light curtain
- That an error was detected by one of the OSSDs
- Interference light has been detected
If an error occurs, the OSSD remains in the OFF state and this state can only be returned to the ON state after the safety light grid has been successfully restarted.
The PSEN op4F-SL series safety light grids have the following features
- Auto Start
- Monitor start
- EDM (when connected to a relay with positive guided contact)
- Cascade
Transmitters and receivers are electrically connected by cables with M12 connectors assigned to the LED-side transmitters and receivers, respectively.
Automatic start
When the safety light curtain is switched on, the safety light curtain is automatically activated and the OSSD switches to the on state under the following conditions
- That both OSSDs are correctly wired
- That there are no faults
- That the protect field is cleared
If the protected field is violated, the OSSD switches to the off state.
Safety distance
The minimum distance between the safety light curtain and the hazardous machine part should be such that the operator cannot reach the hazardous area until the hazardous machine part stops operating.
According to the EN ISO 13855 standard, this distance is determined by three factors:
- Response time for safety light curtains
It corresponds to the interval between the interruption of the beam and the change of the OSSD to the off state
- Machine downtime
Interval between the change of OSSD to OFF state and the cessation of hazardous machine motion (including the reaction time of the connected relay) - Approach speed
Velocity at which the detected object approaches the hazardous area (mm/s)
The general formula for minimum distances according to EN ISO 13855 is as follows
S = K * (t1 + t2) + C |
- S=Minimum distance from the start of the protective field to the source of the hazard (mm).
- K=Velocity at which the detected object approaches the hazardous area (mm/s)
K = 1600 mm/s when S > 500 mm
K = 2000 mm/s when S ≤ 500 mm - t1=Safety light curtain response time in seconds)
Time until the signal at the OSSD output of the safety light curtain changes if the protective field is violated - t2=Machine down time(sec)
Time from OSSD output signal change to machine stop - C=Additional distance for safety light grids with finger protection
Several adjacent safety light grids
The placement of multiple adjacent safety light grids can be accomplished in a variety of ways; be aware of the surrounding conditions.
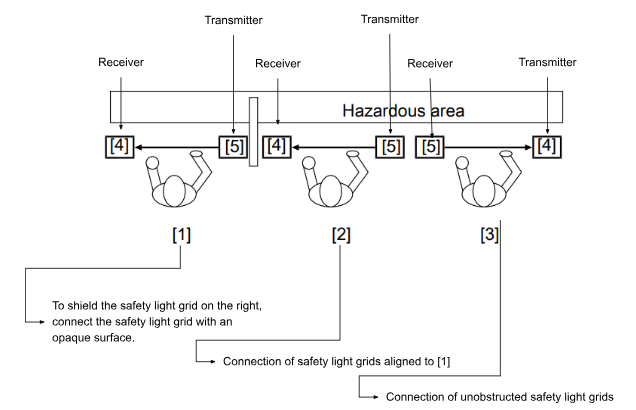
Wiring
There are various guidelines for wiring to safety lights and curtains.For example,
- Keep the terminals for connection to the evaluation device in a lockable control cabinet. This will prevent unauthorized modifications.
- Ensure that the test pulse duration is correctly handled by the evaluation device.
- Do not lay connecting cables near or in contact with cables carrying high or volatile currents.
- Use separate cables to connect wires to OSSDs of different safety light curtains or safety switches.
Connector pin assignment
Electrical connections between transmitters and receivers are made with M12 connectors.
transmitters
receivers
SFB-EC-8M12-IOP?
The Safety Field Box SFB-EC-8M12-IOP is designed for connecting up to eight safety switchgear units with parallel IO signals to an EtherCAT® / FSoE network. In addition, up to four BDF200-FB control panels can be connected to device ports X4 to X7.
Safety signals from the connected safety switchgear are transferred to the safety controller via the safety fieldbus for evaluation. In large safety applications, several field boxes can be connected in series to the power supply and the fieldbus.
The non-safety IO signals connected to the device are then connected to the control system via a fieldbus.
How to Read the Module Number?
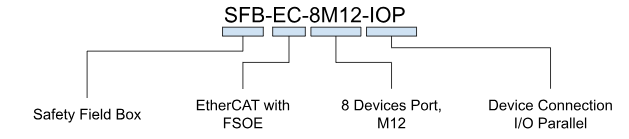
Layout
This is the Layout for SFB-EC-8M12-IOP.
Safety inputs and test pulse outputs
The SFB-EC-8M12-IOP has two safety inputs and two test pulse outputs to provide dry contacts for each of the eight device ports X0 to X7.
These safety inputs can be used for the following applications
- 1-channel safety switch with dry NC contact (1oo1)
- Cross-fault monitoring to all other safety inputs of the field box
- Debounce filter/stability time filter for input signals
- Contact supply by test pulse output with 1 ms test pulse duration and 500 ms test pulse interval
- 2-channel safety switch with dry NC contacts (1oo2)
- Cross-fault monitoring to all other safety inputs of the field box
- Debounce filter/stability time filter for input signals
- Contact supply via test pulse output (test pulse duration 1 ms, test pulse interval 500 ms)
- 2-channel safety switch (1oo2) with 24V-PNP solid-state output (OSSD)
- No monitoring of equipment connection cable crossing faults by field box
- Debounce filter/stability time filter for input signals
- 24 VDC without test pulse on the safety input of the safety switchgear
- Negative test pulse length when switching on OSSD
- Negative test pulses of 10 µs to 1 ms with an interval of 20 ms to 120 s must be transmitted.
Safety outputs
The SFB-EC-8M12-IOP has safety digital outputs on each of the eight device ports X0 to X7 to control loads up to 0.8 A and a configurable safety signal output to control two channel safety inputs up to 15 mA.
These safety outputs can be used for the following applications
- Safety output with one wire (digital output DO)
- Safety digital outputs (PP switching) with max. PL d
- Can be used e.g. with solenoids in interlocks
- Test outputs, short circuit and overload protection
- 2-wire safety output (digital output DO and test pulse output Y1)
- Safety digital outputs up to PL e (2P switching), for control
- Example: Interlock with 2-channel lock function
- Example: 2-channel control of safety relay modules (e.g. SRB-E-301ST)
- Test output, short-circuit and overload protection
Diagnostic input / FB interface
The SFB-EC-8M12-IOP has one diagnostic input for each of the eight device ports X0 to X7 for status signals of the connected safety switchgear.
On the four device ports X4 – X7, the FB interface is additionally integrated into this input. Non-safety signals from command and signaling devices such as BDF200-FB can be transmitted via the single-wire FB interface. The FB interface automatically detects if safety switchgear is integrated.
FailSafe over EtherCAT® communication
FailSafe over EtherCAT® (FSoE) is a functionally safe extension of the standard communication via EtherCAT®. Communications based on FSoE are secure against tampering, transmission errors, changes in the telegram sequence, etc.
And the Safety Field Box SFB-EC is an FSoE module in the EtherCAT® network. The module establishes safety communication with the FSoE master and transmits safety data via “FSoE” and functional data via “EtherCAT®”.
FSoE Address
The rotary switch on the SFB-EC-8M12-IOP can be used to set the FSoE address.
EtherCAT® Linear topology
SFB-EC supports linear topology.
System Layout SFB-EC
Here is an example of a typical system layout and wiring for safety switchgear.
Configurable functions SFB-EC
The Safety Field Box SFB-EC offers a choice of four different configurations (types) for each device port. The parameter data sets (types) are used to configure the device ports for different safety switchgear.
A filter/stability time filter is built in for all safety inputs. The parameters for the stability time filter are fixed for different parameter data set types.
Parameter data set Type A, safety monitoring 1oo2
Cross Fault Detection: Off / Safety switchgear handles cross fault detection.
- For electronic safety switches and sensors with 2-channel OSSD output
- For electronic solenoid interlocks, 2-channel OSSD output, suitable for 1-wire control with unlock function
Parameter data set Type B, safety monitoring 1oo2
Cross Fault Detection: Off / Safety switchgear handles cross fault detection.
- For electronic solenoid interlocks with 2-channel OSSD output and 2-wire control of the unlock function
- For safety relay module (SRB-E) with 2-channel safety input
Parameter data set Type C, safety monitoring 1oo2
Cross Fault Detection: ON / SFB handles cross fault detection.
- For electromechanical safety switches and sensors with 2 NC contacts
- For electromechanical solenoid interlocks with 2 NC contacts and 1-wire control of the unlocking function
Parameter data set Type D, safety monitoring 1oo1
Cross Fault Detection: ON / SFB handles cross fault detection.
- For 2 individual electromechanical safety switches with 1 NC contact
Description stable time filter
Stable time filters are used for bouncing safeguards. The stable time filter automatically detects when the bouncing safeguard has reached a stopped state, in other words, a “stable” state.
After a stable period of time, the safety function is turned on when a constant switch-on signal is received on both inputs.
And safety switchgear with contacts requires a stability time filter. In safety switchgear with electronic OSSD, the output signal is usually filtered internally.
Wiring Exmaple
Type A: Safety sensor with electronic OSSD, monitoring 1oo2
Type A: Safety sensor with electronic OSSD, monitoring 1oo2
Type C: solenoid interlock equivalent to dry contact, monitoring 1oo2
Type C: Safety switch equivalent to dry contact, monitoring 1oo2
Type D: 1 or 2 safety switches, 1 channel with dry contact, monitoring 1oo1
X0-X7
This is the Layout for X0-X7 of SFB-EC-8M12-IOP.
Power
This is the Layout of Power Port of SFB-EC-8M12-IOP.
Web server
The SFB-EC has an integrated WebServer for displaying status and diagnostic data. To access the SFB’s WebServer, the device’s IP settings must be configured by the EoE service.
AZM40Z-I2-ST-1P2P?
The AZM40 has a unique locking feature. This clamping principle has several advantages. The locking bolt and actuator are connected only by chamfered surfaces, which facilitates lateral force compensation.
Before you use..
Do not use solenoid interlocks as end stops.Always remove that lock.
Layout
This is the door lock Layout for AZM40.
- Optimized for mounting on 40 mm profiles
- Symmetrical mounting, can be mounted on both sides
- LEDs visible from three directions
- Series wiring without lowering the safety level
- Locking monitoring of actuators or guards
- Use with RFID Transponder
In addition, the clamp lock allows the RFID sensor to be centered on the opposite side of the locking bolt. This allows multiple devices to be installed side by side, less susceptible to errors from external RFID fields or other RFID systems.
Actuator coding
Individually coded solenoid interlocks and actuators require the following Teach-in procedures
- Turn off the voltage supply to the solenoid interlock once and turn it on again.
- The actuator is recognized in the detection range. The teach-in procedure is signalled by a solenoid interlock, green LED off, red LED on, yellow LED blinking (1 Hz).
- After 10 seconds, a short periodic yellow blink (3 Hz) requests the switch-off of the working voltage of the solenoid interlock.Note that if the voltage is not switched off within 5 minutes, the solenoid interlock cancels the “teach-in” procedure and signals the malfunction with 5 red flashes.
- After reapplying the operating voltage, the actuator must be detected again to validate the taught actuator code. In this way, the activated code is definitively saved.
GUARD LOCKING MONITORED
The safety output of the AZM40Z solenoid interlock is only enabled when the safety guard is closed and the interlock is locked. This is the AZM40Z operating flow.
LED
Continuous self-test ensures the functionality of the solenoid interlocks and the 2-channel safety outputs. Errors on the safety outputs, including short circuits, are notified by different colors or flashing pulses of the integrated three-color diagnostic LEDs. Common errors such as excessive ambient temperatures are also detected and indicated.
Wiring example
Voltage is supplied to the safety inputs of both end-of-chain safety components (considered from the safety monitoring module). The safety outputs of the first safety component are wired to the safety monitoring module.
Connector
AZM40Z is an 8-pin M12 Connector.
Manual release
For installation and maintenance purposes, the solenoid interlock can be unlocked while de-energized. The solenoid interlock is released by turning the auxiliary release counterclockwise.The normal locking function is only restored after the manual release is returned to its original position.
Magnet control
The bistable interlock is released by setting the IN signal (=24V) operation. If the IN signal is not set (=0V), the solenoid interlock is locked as long as the correct actuator is inserted in the solenoid interlock.
Implementation
Wiring
This is the wiring in this article.
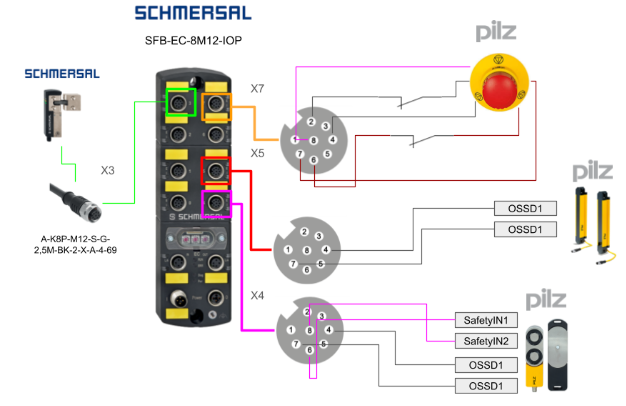
TwinCAT Side
We will start to build the TwinCAT3 project side.
Download ESI File
Download the ESI File for Schmersal’s SFB-EC-8M12-IOP from the link below.
https://products.schmersal.com/en_IO/sfb-ec-8m12-iop-103047531.html
Install ESI File
Store the ESI File downloaded earlier in the following Directory.
(I am using TwinCAT3 4026)
C:\Program Files (x86)\Beckhoff\TwinCAT\3.1\Config\Io\EtherCAT
Reload ESI File
Start TwinCAT3 and reload the ESI File at Extensions>TwinCAT>EtherCAT Devices>Reload Device Descriptions.
Add EtherCAT Master
To add an EtherCAT Master, go to I/O>Devices>Add New Item.
Set the Ethernet Interface to be used as EtherCAT Master.In this case, we will use Ethernet 2, but the RT Ethernet Driver is not yet installed, so click on that Interface.
Click Install.
So now I can configure Ethernet2.
Done!
Scan
The next step is to use EtherCAT’s Scan function to search for EtherCAT Slaves in the network.
Done!We were able to detect Beckhoff’s EtherCAT CouplerEK1101 and Schmersal’s SFB-EC-8M12-IOP.
EoE Configuration
Enable the EoE (Ethernet Over EtherCAT) function of Schmersal’s SFB-EC-8M12-IOP to access the webserver.
Click on EtherCAT>Advanced Settings.
This is the Advanced Settings screen of the EtherCAT Node.
Go to Mailbox>EoE and set the IP address to match your application.
Add PLC
Next, to add a PLC project, go to PLC>Add new Item.
Select Standard PLC Project and add it with >Add.
Add GVL
Now add the Global Variable List to the PLC project.
Enter a GVL name and proceed with Add.
Define non-safety variables for SFB-EC-8M12-IOP and RUN/ACK variables to be sent to EL6910, etc. in the GVL.
{attribute ‘qualified_only’} VAR_GLOBAL RUN AT %Q*:BOOL; Ack AT %Q*:BOOL; DoorLockOSSD AT %I*:BOOL; SFB_PortQualifier AT %I*:DUT_8BitDevices; SFB_DiagnosisData AT %I*:DUT_SFBDiagnosisData; ErroCode AT %I*:USINT; SFB_Ack AT %Q*:BOOL; END_VAR |
POU
Here is a program to send a 500ms reset pulse to the SFB-EC-8M12-IOP.
PROGRAM MAIN VAR xON:BOOL; Ton1:TON; END_VAR GVL.SFB_Ack:=xON ; Ton1( IN:=xON ,PT:=T#500MS ); IF Ton1.Q THEN xON:=FALSE; END_IF |
Build
Compile the project under Build>Build Solution.
Link
The next step is Mapping the Port Qualifier and diagnostic information of the SFB-EC-8M12-IOP and the GVL of the PLC project.
If you want to map variables together, select all variables and click >Change Multi Link.
Done!Mapped variables are marked with an X.
Add Safety Project
The next step is to build the EL6910 side.
Add a Safety project under SAFETY>Add New Item.
Select TwinCAT Safety Project Preconfigured ErrAck and add it with >Add.
Select Hardware Safety PLC as the Target System and OK to create the project.
Configure Target System
Safety You must configure the FSoE Master to be used for your project, click on Target System.
This is the Target System settings screen.
Target System
Set EL6910 from Drop-list in Target System.
Select Physical Device
Next, click on the Physical Device button.
Configure the EL6910 in the EtherCAT network.
Done!FSoE Address and other information for EL6910 was also obtained.
Add Alias Devices Schmersal
Now add Schmersal’s SFB-EC-8M12-IOP to the Safety project.
Alias Devices>Add>New item to insert a new device.
Let’s add Safety>EtherCAT>K.A Schmersal GmbH>0x000A001.
Done!
We will now set the Connection and Application parameters for Schmersal.
FSoE Address
The FSoE address should be set according to the rotary switch setting of Schmersal’s SFB-EC-8M12-IOP.
Physical Device
Next, click on Physical Device and select the SFB-EC-8M12-IOP in the EtherCAT network.
Done!
Watchdog(ms)
Set Conn-Id and Watchdog(ms) in the Conenction Tab according to your application.
Safety Paramter
Open the Safety Parameters Tab and set the operation mode for each Port.
You can make the appropriate settings from the Drop-List by double-clicking on the Value column for each Port.
X3
PortX3 is connected to Schmersal’s AZM40Z-I2-ST-1P2P.
Set PortX3 to Mode A.
X4
X4 is connected to the Pilz door lock.
PortX4 is set to Mode B.
X5
X5 is connected to Pilz safety light curtains.
PortX5 is set to Mode A.
X7
X7 is connected to the emergency stop input/output.
PortX7 is set to Mode C.
Add Normal
Create Non-Safety data to obtain OSSD output for Normal TwinCAT Runtime Run/ACK or Door lock.
Add Digital Input/Output in Standard.
Done!
For example, if you want to connect a RUN variable to a TwinCAT PLC Runtime variable, click on the Linked to button.
Select GVL.Run.
Done!Follow the same procedure for other variables.
Add Global Variable List
Click GVLs>Add>Global Variable List to define variables for the safety program.
Add variables with the + button.
Done!
Click Assignment to set the relevant safety variables and the variables to be connected.
This variable is tied to Port X7.Input X1 AND X2 of SFB-EC-8M12-IOP (i.e., the signal that turns on Port7’s X1 and X2 inputs simultaneously).
Done!The same procedure should be used to define other variables.
- gX7ESTOP:Port X7 emergency stop input signal
- gX7Output:Output signal of Port X7
- gRUN: Safety Group RUN signal
- gX5OSDD:OSSD input signal of Port X5
- gX4Out:Safety Output signal of Port X4
- gX3Out:Door lock signal of Port X3
- gX3OSSD:Door lock OSSD signal of Port X3
- gDOUT:Port X3 OSSD signal passed to Normal TwinCAT Runtime
Safety Program
To create the Safety program, open TwinSafeGroup1.sal.
Here is the safety program we created for this article.
Network1
Network1 converts safety input signals to internal variables via SafeDecouple FB.
Also, the OSSD signal connected to Port X5 is turned on with a delay by SafetTon.
Network2
Network 2 uses SafetAnd FB to output the ESTOP/OSSD signal when it arrives.
Network3
Finally, SafeDecouple is used one more time to reflect the results of internal variables in the safe output.
Link Run Variables
Run/Stop Variable must be Mapped, click Variable Mapping>Group Ports>Assignment.After that, connect the Non-Safety Variable gRUN that you defined earlier.
Check Safety Program
Now that you have finished creating the safety program, compile the safety project using the button in the red frame.
Download Safety Program
Download the compiled safety program to the EL6910.
Enter your Login information and press Next to proceed.
Select Complete Project Data and press Next to proceed.
Check the Download result and press Next to proceed.
Check the status of the project and proceed with Next.
Enter your Password again and restart EL6910.
Active Configuration
Download the TwinCAT project to the PLC.
OK to proceed.
Switch TwinCAT3 to Run Mode.
Login
Download the program in Login.
Proceed with Yes.
最後はPlayボタンをクリックしPLCプログラムをスタートします。
Result
Here is a video of EL6910 working with Schmersal SFB-EC-8M12-IOP and emergency stop.
Beckhoff.EL6910 With Schmersal SFB-EC-8M12-IOP And ESTOP
Here is a video of EL6910 working with Schmersal SFB-EC-8M12-IOP and Pilz Light Curtain.
Beckhoff.EL6910 with Schmersal SFB-EC-8M12-IOP And pilz light curtain
Here is a video of EL6910 working with Schmersal SFB-EC-8M12-IOP and Pilz Door Lock.
Beckhoff.EL6910 With Schmersal SFB-EC-8M12-IOP And Pilz Door Lock
Here is a video of EL6910 working with Schmersal SFB-EC-8M12-IOP and Schmersal AZM40Z-I2-ST-1P2P door lock.