In this article, PROFIsafe is set up with TRUCK’s TBPN-L1-FDIO1-2IOL and Siemens’ S71516-F, and the module is wired with Keyence’s GL-R SERIES safety light curtains.
Let’s enjoy FA!
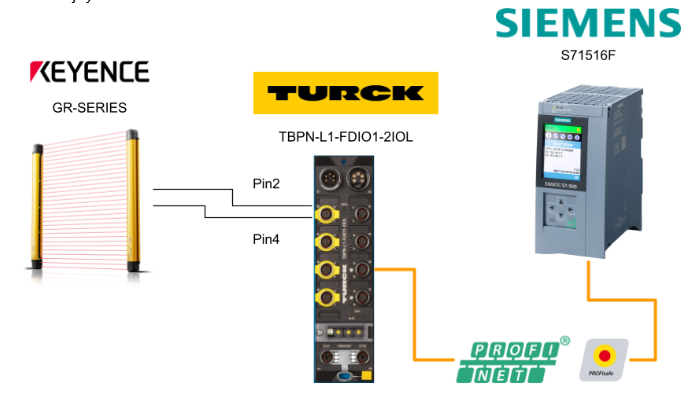
TBPN-L…-FDIO1-2IOL?
TBPN-L… -FDIO1-2IOL is a distributed safety module for PROFIsafe. It collects field signals and transmits them securely to the PROFIsafe master. 40… With a temperature range of +70 °C and a protection class of IP67/IP69K, this module can be used directly on machines that require an industrial environment.
The modules are used to control signaling devices used for the protection of people, materials, and machines, for example, emergency stop buttons, position switches, and OSSDs.
For non-safety-related features, Safety-Hybrid-Modul has an additional universal input channel, two IO-Link master channels for connecting IO-Link sensors, and an IO-Link hub that can expand to up to 32 I/O signals.
TBPN-L…The -FDIO1-2IOL can be used for the following applications:
- Applications up to SIL 3 (according to IEC 61508)
- Applications up to SIL CL3 (according to EN 62061)
- Applications up to category 4 and performance level e in accordance with EN ISO 13849-1
Layout
This is the Layout for TBPN-L…-FDIO1-2IOL.
Safety function
TBPN-L…The -FDIO1-2IOL provides two secure digital SIL3 inputs (FDI) and two SIL3 connectors (FDX) that can be configured as inputs or outputs.
The following devices can be connected to the safety input as:
- 1- and 2-channel safety switches and sensors
- Contact-type switches (e.g., emergency switches, protective door switches)
- Sensors with OSSD switching output
- OSSD sensors with antivalent switching
- Two safety SIL3 outputs are available with PP- or PM-switching
Safe Status
In the safe state, the device output is in LOW state (0).The input feeds back the LOW state (0) to logic.
- Fatal errors
- Mis-wiring of outputs (capacitive loads, energy recovery, etc.)
- Short circuit at line control output T2
- Wrong power supply
- Strong EMC disturbances
- Internal device error
Safety inputs (FDI)
The safety input is suitable for connecting safety-related sensors:
- Up to four 2-channel safety switches and sensors
- Switches with contacts (e.g., emergency switches, protective door switches)
- Sensors with OSSD switch output with test pulse
- Sensor with OSSD switch output without test pulse)
Safety outputs (FDO)
The safe SIL3 output can be PP- or PM-switched, resulting in a maximum of 2-channel safe output (outputs are supplied via V1).
Universal standard I/Os
Unsafe universal I/O is available in C4/C5.
IO-Link master channels
Unsafe IO-Link master channels are available on C6️/C7.
Power Supply
X1/X2 are ports for power supply.
F address
The TBPN-L…-FDIO1-2IOL has three rotary switches to set the F-Address for Profisafe communication.
Safe electronic input (OSSD)
Since the GL-R SERIES safety light curtain from Keyence is used in this article, the safety input must be set as an OSSD input.With this connection and the corresponding parameter settings, the pulses on pins 1 and 5 will be turned off; the supply voltage on pin 5 will be turned on again.
To avoid errors, do not use a 5-pin cable for the sensor.
Input Data
This is the input data Mapping for TBPN-L…-FDIO1-2IOL.
Output Data
This is the output data Mapping for TBPN-L…-FDIO1-2IOL.
GL-R Series?
The product used in this article is the GL-R SERIES safety light curtain from Keyence.Before proceeding with the actual article, I will explain a little about the wiring and other details.
Layout
Here is an outline drawing of the GL-R SEIRES.
Wiring
Here is the wiring diagram for GL-R SERIES.
OSSD?
OSSD is a safety-related control output and is connected to an external device (load) such as an FSD or MPCE, etc. GL-R generates self-diagnostic signals in the internal control circuit to diagnose the output circuit (OSSD).These signals periodically and temporarily turn off the OSSD when no interrupt is present in the detection zone.
When a feedback signal (OFF signal) is input to the internal control circuit by self-diagnosis, GLR determines that the output circuit is operating normally.If this OFF signal does not return to the internal control circuit, the GL-R determines that there is an error in the output circuit or wiring and enters an error state.
For wiring between GL-R and safety-related parts of the machine control system, be sure to wire both OSSD 1 and OSSD 2 to safety-related parts of the machine control system to ensure safety.If only one OSSD is wired to the safety-related part of the machine control system, serious damage, including serious injury or death, could occur to the machine operator in the unlikely event of an OSSD malfunction.
Implementation
Turkc Side
First build TURCK’s ProfisafeIO TBPN-L…-FDIO1-2IOL.
Wiring
Here is the wiring for TURCK’s ProfisafeIO TBPN-L…-FDIO1-2IOL and Keyence’s GL-R SEIRES safety light curtain.
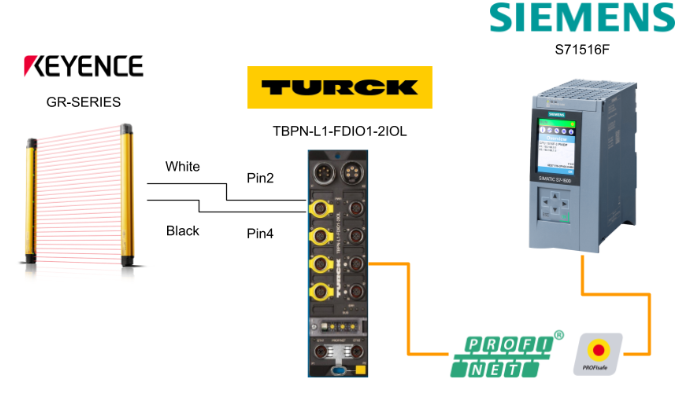
Install the Tools
Now download Turck’s Safety Configurator from the following site.
Note that you will need a coupon code to download the software, so please contact your local Turck Office.
https://www.turck.jp/ja/product/SW_Turck_Safety_Configurator
Double-click Install.exe to begin software installation.
Choose your language and proceed with Install.
Just a second…
Proceed with Next>.
Accept the license and proceed with Next.
Proceed with Next.
Start installation.
Just a mins..
Done!
Close the installer.
Next, you will be asked to enter your license and proceed with Yes.
Select Coupon Code and enter the Coupon Code you used when you downloaded the software earlier.
Just a mins..
Done!
Create your project
Start Turck’s Safety Configurator.
Create a new Workspace at File>New>New Workspace.
Sets the Workspace storage location.
Check and proceed with OK.
Select the Safety IO Block to be used in the project.
PC->Monitor
Click on PC->Monitor in Tools and you can Download Configuration to the module.
Set Network Interface with Yes.
The Interface settings screen appears.
Configure Ethernet and click on Search for device to search for Turck devices in the network.
複数のNetwork Interfaceが接続されてる場合、ツールからエラーが表示されるので、使用しないInterfaceを無効にしましょう。
Done!Turck device found.
Click on the button in the red frame to confirm the TURCK device.
TURCKデバイスはこのように点滅します。
https://youtube.com/shorts/tXK0bZZvBF8
Click the Setup button to configure the TURCK device.
IP address, device name, etc. can be set from this screen.
You can change the Profient device name by checking the Changer device name checkbox.
Next, set the IP address according to your application.
Done!Finally, click the OK button to apply the settings.
Reboot the device with Yes.
Click the Search button to search for the device again.
Done!IP address will be changed.
Configuration
Now we can set the Module.
Click on the module>edit safety monitor.
Here is the properties screen.
IO Configuration
The next step is to configure the safety inputs and outputs of the IO module.
Safety input FDI 0/1 is connected to OSSD, but Default is an E-STOP connection.To change this setting, click on the “Expert” button.
I/O Type
Set I/O Type to Safe input (OSSD).
Graphic
Change the Graphic into a device that is connected to real hardware.
Device Type
Match Device Type to the application.
Output
Click on Output assogment and set the Fieldbus Bit for Profinet/Profisafe.
Data to be exchanged with Profinet/Profisafe Controller can be set from this screen.
Set F-CPU Input 17/18 to 1.6 and 1.7 of Profisafe.
It links to Bit 6 and Bit 7 of 1 Byte of Profisafe F-Host.
Also set the same F-CPU Input 17/18 to 0.6 and 0.7 of Fieldbus.
It links with 0 Byte ‘s 6th and 7th Bit of Profisafe F-Host.
Safety Program
Next, let’s create a simple safety program.Make sure the OSSD input in Keyence is OFF Delay and then Feedback to the Profinet/Profisafe device in F-Host.
Send
Finally, click PC->Monitor and download the project to the module.
Set the Safety Password.
Please wait a moment…
Done!
Enter the name and Password of the engineer who changed the project.
WebServer
In addition, TURCK’s Profisafe IO module has a Web Server to check the current module information.
Siemens Side
The next step is to build the Siemens side.
Download GSDML File
Download the GSDML File for the TURCK Profisafe IO module from the link below.
https://www.turck.de/en/product/6814053
New Project
Start TIA, Start>Create new project>enter a project name and Create to create a new project.
Click on Project view.
This is the TIA project creation screen.
Install GSDML
Click Options>Manage general station description files (GSD).
The GSDML administration screen will appear and click on the … button.
Select the GSDML Folder that was just downloaded.
Done!GSDML File is found, install GSDML File with Install.
Done!
Add PLC
Let’s add a new Siemens PLC under Project>Add new device.
If you do not know the type of CPU you are currently using, set Unspecified CPU 1500.
Done!Next, use “Detect” to search for S71500 CPUs in the network.
Click Start Search to search for devices on the network.
Then select the appropriate CPU.
Proceed with Connect.
Security Setting
Security settings related to CPU from TIA V18 must be pre configured.Since this is not an actual operation, all security settings are disabled in this case.
Protects the PLC configuration data from the TIA.Uncheck the “Protects the PLC configuration data from the TIA.
Only allow secure… Uncheck the “Only allow secure.” checkbox and click Next>> to proceed.
Set to Full access with no password and press Next>> to proceed.
Check one last time and save the settings with Finish.
Result
Done!S71516F-3 has been added.
F-Activation
Let’s enable the Safety function by Fail-safe>F-activation to enable the F-Host function of S71516F-3.
Program
We will now create a program for Siemens.
PLC Data Type
DUT_Array_2bytes
This is a 2 Bytes long structure.
DUT_Array_4bytes
This is a 4 Bytes long structure.
DUT_Array_6bytes
This is a 6 Bytes long structure.
DUT_Array_8bytes
This is an 8 Bytes long structure.
DUT_Array_14bytes
This is a 14 Bytes long structure.
DUT_Array_64bytes
This is a 64 Bytes long structure.
DUT_diagnostic
This is the structure for the diagnostic Slot used when communicating with TBPN-L…-FDIO1-2IOL and Profinet.
DUT_IOLINKEVENT
This is the structure for the Slot for IOLink evento used when communicating with TBPN-L…-FDIO1-2IOL and Profinet.
DUT_SafetyStatus
This is the structure for the Slot of Profisafe Status used when communicating Profinet with TBPN-L…-FDIO1-2IOL.
DUT_SafetyStatus_Connector
This is a structure that summarizes the status of each Port in Profisafe Status.
DUT_SafetyStatus_FConfig
This is the structure that summarizes F_Config for Profisafe Status.
DUT_SafetyStatus_SafetyUnit
This is the structure that summarizes the safety Unit of Profisafe Status.
DUT_TBPN_L1_Datas
The last one is DUT_TBPN_L1_Datas, which summarizes the structures defined earlier.
sDUT_Array_1bytes
This is a safety type structure of length 1 Bytes.
sDUT_Array_2bytes
This is a safety type structure of length 2 Bytes.
Tags
Let’s define Tag using the structure we just created.
Main_Safety_RTG1
The next step is to create a safety program.
Network1 is the logic that resets the TBPN-L1-FDIO1-2IOL when a QBAD occurs.
Network2 calls the Function Block that resets all Safety Devices.
Network3 makes visible the Safety Light Curtain signal from TBPN-L1-FDIO1-2IOL.
DB_Data
This is a Data Block that stores information on TBPN-L1-FDIO1-2IOL.
Function Block
FB_TBPN_L1_Diagnostic
This is a Function Block to decode the diagnostic information of TBPN-L1-FDIO1-2IOL into a structure.
FB_TBPN_L1_IOLinkEvent
This is a Function Block to decode the IOLINK Event of TBPN-L1-FDIO1-2IOL into a structure.
FB_TBPN_L1_SafetyStatus_Connector
This is a Function Block to decode the Port information of TBPN-L1-FDIO1-2IOL into a structure.
FB_TBPN_L1_SafetyStatus_FConfig
This is a Function Block to decode the F-Config information of TBPN-L1-FDIO1-2IOL into a structure.
FB_TBPN_L1_SafetyStatus_ProfiSAFEErrorCode
This is a Function Block to decode ProfiSAFE error information of TBPN-L1-FDIO1-2IOL into a structure.
FB_TBPN_L1_SafetyStatus_SafetyUnit
This is a Function Block to decode the Safety Unit information of TBPN-L1-FDIO1-2IOL into a structure.
FB_TBPN_L1_SafetyStatus
This is a Function Block to decode the Safety information of TBPN-L1-FDIO1-2IOL into a structure.
FB_TBPN_L1
Finally, call the Function Block you just created together.
Main OB1
Finally, call FB_TBPN_L1 for OB1.
Add Turck TBPN-L1-FDIO1-2IOL Devices
Add TURCK’s TBPN-L1-FDIO1-2IOL to the Profinet network.
Add the appropriate GSDML File for the Firmware of TBPN-L1-FDIO1-2IOL.
Done!
Assign Network
The next step is to assign TURCK’s TBPN-L1-FDIO1-2IOL to Profinet.
Done!
Assign IP
Next, set the IP address.
The IP address of the device is displayed.
Set it up according to your actual application.
Device Name
Profient device names can be set in Properties>PROFINET interface>ETHERNET interface.
If you want to change the device name automatically generated by the TIA tool, uncheck the “Generate PROFINET devicer name automatically” checkbox and enter the PROFINET device namePROFINET device name.
Configure Slot
Now set up each Slot of TBPN-L1-FDIO1-2IOL.
Let’s add a Module to the Slot of TBPN-L1-FDIO1-2IOL in Hardware Catalog>Catalog.
Done!
Profisafe Address
Profisafe communication requires the F-Address of the device to match that of the actual device.Select the slot with the yellow ICON > PROFIsafe > F_Dest_Add setting to match the actual device.
CRC
Next, the parameter CRC must be set for the TIA project.
We just received the parameter CRC values from the TURCK Safety tool.
Enter its CRC value in F_iPar_CRC.
Assign device name
Finally, assign the device name to the actual device.
Search for devices in the Profinet network in the Update list.
Select TBPN-L1-FDIO1-2IOL and click >Assign name.
Done!
Download
Download the Hardware Configuration and program to the CPU.
Result
If the CRC value is not set correctly, the TBPN-L1-FDIO1-2IOL will show a CRC Mismatch error.
There is no QBAD signal on TBPN-L1-FDIO1-2IOL and the module is in good condition.
There are no Profinet or network errors.
You can see the actual operation in this video.
Downlaod Project
You can download the Sample project from this link.
https://github.com/soup01Threes/Siemens/blob/main/Project_TestingWIthTurck_TBPN-L1-FDIO1-2IOL.zap18